FAQ
Frequently asked questions
Everything you need to know
Material
Fairmat has conducted a simplified LCA. While this is not a certified one, a simplified LCA gives estimates of a product’s environmental footprint. Based on the results of the simplified LCA, Fairmat Laminates have a lower environmental load than virgin CFRP. Fairmat Laminates offer a lighter and less impacting solution than thermal recycled carbon fiber and glass fiber.
The Fairmat process can obtain different performance ranges depending on the orientation and arrangement of the reinforcements.. Typically, for exposure in a single direction of space, the material exhibits a flexural modulus of 86 GPa, higher than aluminum. And a tensile modulus of 80 GPa.
The weight of the material will depend on its thickness. However, its low density (1.38) makes it lighter than other materials, such as aluminum, at equivalent thickness. For more information, refer to the material datasheet.
The Fairmat material can have several thicknesses. It is possible to supply thicker parts on small parts.
Yes, thanks to the adapted resin. Fairmat materials are very durable.
Yes, the material is recyclable
We offer a recycled composite material, and this implies several things. Various resins can be use, which allows Fairmat to adapt its new composite to several industries or applications. We need to guarantee a high performance of our material according to various properties (strength, bending, lightness, etc.). Therefore, we can obtain such characteristics through the programs supported by artificial intelligence and machine science that will give an output without variation and with superior results. Due to confidentiality, we will not go into details here.
Depending on the application and the expected properties/characteristics, it is possible to use different matrices, thermoset or thermoplastic. For example, an epoxy resin will provide good mechanical properties and good resistance to moisture and chemicals.
Fairmat materials are suitable for a variety of industries such as sporting goods solutions (padel rackets, shoes insoles, helmets, skis …), mobility (parts in automotive), consumer electronics (casing, etc.), and smart city solutions (hydrogen fuel cells).
Molding parameters will depend on the resin used. Some resins can be molded cold, but other resins, or properties are obtained by increasing the temperature.
Molding parameters will depend on the resin used. Some resins can be molded cold, but other resins, or properties are obtained by increasing the temperature.
Our materials are:
Sustainable: our material emits less CO2 than the materials it replaces (virgin carbon fiber, steel, aluminum)
High-performing: our materials exceed the required physical and mechanical properties found in commonly-used wood, plastic, and metal materials
Lightweight: the weight of our materials is reduced compared to other plastic and metal materials for an equivalent stiffness.
Our standard shape has mainly the form of rectangular plates (laminated). The shape depends on what our customers need to meet its requirements. Fairmat can take the form of a complex shape through a molding process. The only condition is to have the adapted mold.
We have a variety of solutions to cater to the needs of business.
Fairmat redesigns the traditional step-by-step method and builds out the software and robotic solutions to fully automate the manufacturing process. This design and build service can be customized to each clients’ need, both on and off premises. Contact our Sales teams for more information.
It is the European Union Regulation (EC) governing the Registration, Evaluation, Authorization, and Restriction of Chemicals (REACH) that Fairmat products comply with. Our material contains no more than 0.1% by mass of substances of very high concern (SVHC) listed in Annex XIV.
Recycling technic
The Fairmat process has four main steps, each of which involves robotization tools and machine learning programs that allow automated and intelligent work, creating a more efficient technological solution and, above all, guaranteeing the expected outputs:
– Creation of Chips from composite waste
– Add a small amount of resin to form the new matrix
– Molding according to the selected format
– Hardening.
Our automated cutting process allows us to standardize our compounds. We do not shred. We use a smart, low-energy process that helps maintain the integrity and effectiveness of the fiber length. We keep the original resin and carbon fiber together in these compounds.
One Fairfactory is open in France (Nantes), and additionals are coming in the US, Europe & Asia.
Fairmat has conducted a simplified LCA. While it doesn’t result in a certification, a simplified LCA estimates a product’s environmental footprint. Based on the results of the simplified LCA, Fairmat Laminates have a lower environmental load than virgin CFRP. Fairmat Laminates offer a lighter and lower-impact solution than thermal recycled carbon fiber and glass fiber. Fairmat has conducted a Simplified LCA to be able to visualize our impact on the environment and be able to implement changes.
Fairmat has conducted a Simplified LCA. While it doesn’t result in a certification, a simplified LCA estimates a product’s environmental footprint. Based on the results of the simplified LCA, Fairmat’s recycling technology has a much lower environmental impact than thermal recycling (pyrolysis). This lower impact is mostly due to Fairmat’s low energy consumption.
We provide a seamless service and a smooth transition from your existing method. We deliver empty and reusable containers to your site and manage the transport to the Fairfactory to provide you with a virtuous recycling process and avoid CO2 emissions or land pollution.
Waste
Fairmat has developed a recycling solution for carbon fiber and polymer matrix composites. We accept CFRP, in the form of prepreg, pultruded, woven whether they are expired, at the end of their life, or simply in the form of production scraps. We managed to explore new sources of waste coming from the dismantling of aircraft parts.
The waste comes from various industries that use carbon fiber composites, such as aeronautics or wind power. Composites can be recovered at various stages of their life (e.g. scrap, end-of-life products).
No. 95% of carbon fiber composites are currently sent to landfilled or incinerated. Fairmat offers a virtuous alternative to these services provided by large waste recovery companies. Like them, we provide a commercial solution adapted to the needs of our customers while guaranteeing a real ecological advantage.
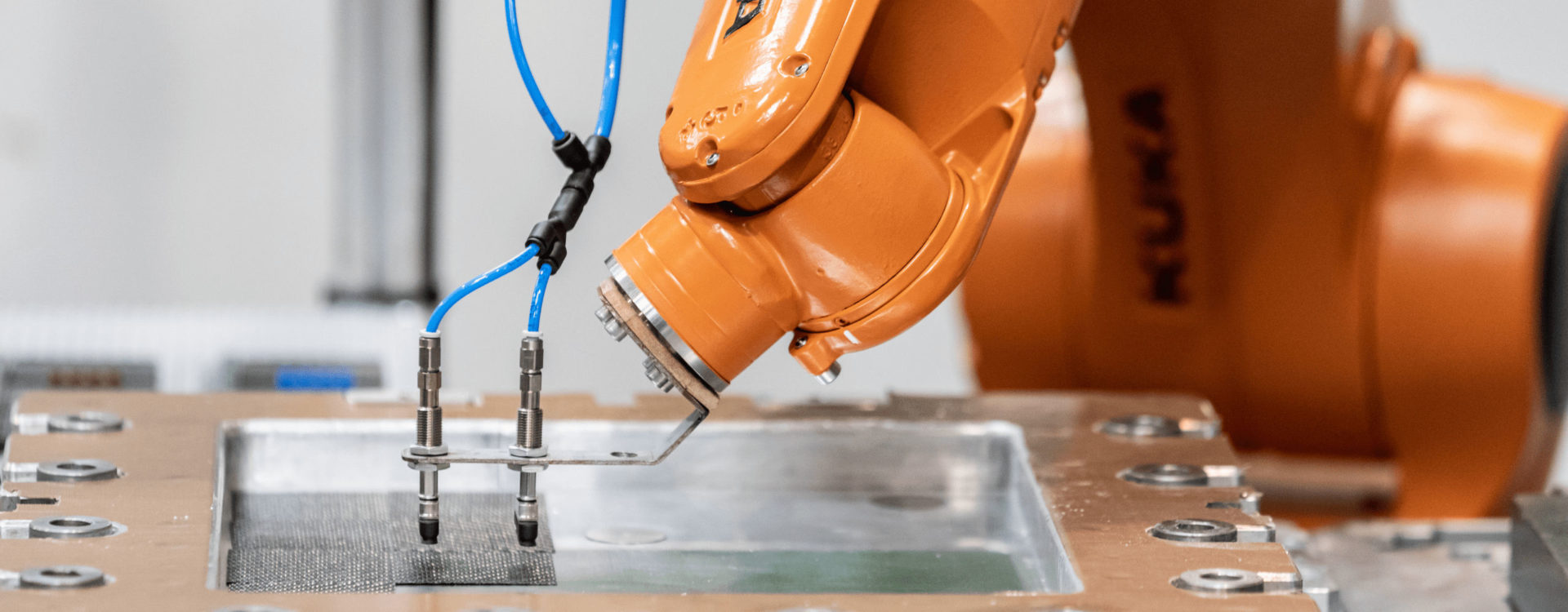